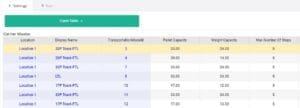
Supply chain management has been in the news. Because of the pandemic and resulting product shortages, the topic has never been more discussed. But the intricacies of supply chain management are beyond the grasp of most. One key solution used to help manage complex supply chains is supply chain planning (SCP).
Supply chain planning is a complex solution. What follows are some key things a newcomer to the supply chain profession, or an interested reader of news headlines, needs to know about SCP technologies, processes, and roles.
Supply chain planning solutions can have a very good payback. The primary payback for demand and supply solutions comes in the form of reducing the amount of raw material, work-in-process, and finished goods inventory a company needs to carry. A network design model figures out where factories and warehouses should be located. Here the savings are based on transportation and facility cost savings.
There are different types of supply chain planning solutions. The key solutions are demand forecasting/inventory optimization, supply planning, and network design.
There is no point in reducing the amount of inventory carried if it results in poor customer service and lost sales. SCP solutions set target service levels, for example 99% for the most important customers and 95% for the rest, and achieves those service level targets at the lowest cost.
Supply chain planning solutions are tradeoff machines. A planner can see how much extra it would cost to take service levels from 95% for all customers to 99%. But it is not just service level and costs that can be traded off. A planner could ask the SCP engine to achieve 95% service, with CO2 emissions under of under a million metric tons at a given factory in the coming month. This would be a three-way tradeoff. Other tradeoffs, to maximize cash on hand or preferred suppliers or customers to do business with, are possible as well.
Supply chain planning takes place at various time horizons. Each time horizon usually has its own model associated with it.
- Long-term planning – often called strategic planning – has a time horizon of 1 – 5 years, and the plans may be reviewed when a new strategic decision needs to be made, or on a quarterly or annually basis. Issues addressed at the strategic planning level include investment in production capabilities, new storage and logistical capacity, supplier agreements, new markets and distribution channels, and introduction of new products. The key solution for this is network design.
- Medium-term planning – known as tactical planning. This is typically monthly planning are plans are created for the next 12 to 24 months. Only the next month’s plan firm. The key solutions are supply planning, based on a broad model of the supply chain, and demand planning. It is embedded in the integrated business planning (IBP) process. IBP seeks to balance the demand forecast with what can be made in the most profitable manner. Some companies are working to engage in IBP planning on a weekly basis. While difficult to do, there is evidence that does result in better planning.
- Short-term planning – known as operational planning. This takes place on a weekly or daily basis, or sometimes even multiple times a day. The IBP plans are sent to the plants with what needs to be manufactured and to distribution on what needs to be shipped to customers. IBP planning is not perfect. No plan is. Customers decide to change or cancel their orders, or machines break down, or ports get backed up. The operational plan seeks to deliver on what has been agreed to in the IBP meeting in the best way possible considering the issues that have arisen. This is typically accomplished with a very detailed supply planning model that models a specific manufacturing plant.
Concurrent planning links execution plans, the plan for what will be made the next few days or weeks, to the longer-term financial plans, often called integrated business plan. As new short-term plans are created, the linkage to the revenue and profitability goals based on the initial IBP plan becomes instantly visible.
Supply and network design models are constraint-based models. In a supply chain you have orders, suppliers, raw materials, machines, customers and other entities as well. Some orders are big, some small. So, order minimums and maximums, are constraints. The orders have products. Different products are made from different raw materials and components. The Bill of Material, how a product is made, and how a product flows through a factory offers a new set of constraints. How long it takes to set up a machine, what the throughput is for different products, introduces other constraints. Customer due dates are a constraint. A big supply model can have over a million constraints on an end-to-end supply chain. There are MANY different types of constraints.
It used to be that these broader supply models used in IBP considered mainly manufacturing and distribution constraints. Now they are considering transportation, supplier contracts, workforce, customer constraints, and many other things in an end-to-end supply chain.
Supply models for operational planning don’t go broad, they go deep. A factory planning solution will model the factory floor set up times by machine for example. The IBP model, the broader network model, might just say on average across all products the throughput is 1,000 units per hour.
Supply chain planning engines “optimize” the schedule. An optimal plan is not a perfect plan. Optimization means that there are so many ways an end-to-end schedule could be set up, that even if the planning engine ran a million years it would still not have looked at all the options. “Optimization” uses clever math to come up with a very, very good solution in a short planning run.
Supply chain planning solutions use a variety of different types of algorithms, as well as machine learning and artificial intelligence, to provide optimal forecasts and plans. Machine learning is one type of solver. It is not the best of all solvers, it is very good for certain types of solves, and not good for other planning problems. SCP vendors need to have a library of algorithms and solver technologies, and then apply the right technology to the right problem.
Even though not all scheduling scenarios are considered, good planning depends upon powerful computers with fast databases. “Scalable” – big fast planning engines – run on specialized databases. In-memory is most common, but graph databases are beginning to be increasingly used.
There are different types of planners. Many companies have demand planners and supply planners. We are starting to see network planners who do both the supply and demand planning. Using network planners does make sense, not just because there are fewer planners, but because there are fewer times a plan must be handed back and forth. Planning is becoming increasingly autonomous. More and more tasks are being taken over by the planning engine, leaving planners the opportunity to run scenarios on only the most important problems.
The supply chain planning software market grew at a double-digit rate over the last year. It is unusual for a mature, multibillion dollar market to grow so fast. Clearly, the pandemic has been a driver. The pandemic has highlighted the need for companies to be agile and resilient. SCP is one key technology for achieving these goals.