When it come to smuggling, drug dealers are taking things to a while new level. Colombian drug smugglers are disguising cocaine as “fake coal” within major bulk consignments to try to dupe port surveillance operations, according to a new report. Anti-narcotics investigators have uncovered substantial amounts of the disguised drugs in the past two years […]
Managing yard and warehouse operations has long been one of the thornier aspects of transportation logistics. A recent conversation with a major distributor of consumer beverages encapsulated many of the most common issues. Yards are a choke point between transportation and warehousing — and wherever you have choke points, you have a higher risk of […]
I am coming to you from the sunny confines of San Diego, CA where I am attending the 2024 Körber Elevate conference. This is my first time attending Körber Elevate, and it did not disappoint, with over 800 attendees, 60 thought provoking sessions, and lots of networking and learning opportunities. The theme this year was […]
While Generative AI has sparked great excitement, a form of artificial intelligence called Causal AI might offer much greater potential. Causal AI offers the tantalizing promise of being able to unravel the intricate web of cause-and-effect relationships that govern business operations. Georgia-Pacific (GP) has demonstrated an application of Causal AI to dramatically improve touchless commerce. […]
After months of anticipation, the day is finally here. On February 4 at the 2024 Grammy Awards, Taylor Swift announced that she would be releasing a new album, which had secretly been in the works for two years. The album, The Tortured Poets Department, was released overnight. But in a shocking twist, just two hours […]
Over the past decade, the main battleground for China’s WMS market has been in the consumption industry; but more recently the battleground has returned to the manufacturing industry. Overseas suppliers have always ruled the top end of the market in this segment. However, local Chinese vendors have been growing rapidly over the past few years […]
Myron Ebell, who headed the Environmental Protection Agency (EPA) transition team for Trump’s first term, says that should Donald Trump and the Republicans defeat President Biden in November’s election, they will seek to dismantle climate legislation. A core target will be the Inflation Reduction Act, the legislation filled with support for clean energy projects and […]
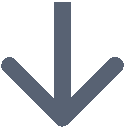