In several industries, pending regulations call for more robust product traceability. Many manufacturers view traceability as a necessary cost, rather than something that brings benefits. However, under no regulatory requirement to do so, Bayer CropScience recently implemented an end-to-end product tracking system solely for the benefits it could provide, particularly to customers at the end of the value chain — in this case, farmers.
Farmers get a better yield if soybeans are treated with chemicals prior to planting. However, the chemicals need to be applied locally, by local distributors and seed treatment companies. This is because after one year, the chances of the seeds germinating decrease greatly. Thus, it makes sense to wait until the seeds are sold before applying the chemicals. If not sold, the seeds can be crushed and made into food. (If the seeds are treated, but don’t sell, they would have to be destroyed.)
Accurate demand planning, which would permit seed treatment at a regional or national level rather than the local level, is not practical. The optimum seed treatment depends on a field’s moisture level, pH level, and other factors that cannot be known with any degree of certainty in typical forecast planning horizons.
Bayer CropScience, with revenues approaching seven billion euros, is a key supplier of seed treatment active ingredients to local seed treatment companies. The company already had the ability to trace all the raw materials used in the company’s production lots backwards from the factory.
However, Bayer CropScience wanted the ability to provide complete stewardship — as well as end-to-end traceability — for the farmers at the end of the value chain. In this context, stewardship means ensuring accurate mixing and application of the chemicals to the seeds. The need for better stewardship has been increasing. New active ingredients require greater mixing precision, with the actual amount of active ingredient specified per seed! Older, more manual methods were just not good enough.
In this application, end-to-end traceability is challenging because each farmer buys small batches from local seed treatment companies. Many of these small companies, not unexpectedly, did not possess the same traceability capabilities as do global manufacturing companies. As a result, recalling an active ingredient could be a time-consuming and far from targeted process. A local distributor might know it had bought a particular active ingredient, but not which specific grower’s seeds used that particular chemical. The result would be a much bigger recall than necessary. Luckily, recalls are rare.
The more exciting capability offered by true end-to-end traceability was improved yields. Most modern combines can be equipped with yield monitors, enabling farmers to know which combination of seed varieties and treatments work best for particular field conditions.
To get to real-time, end-to-end traceability, Bayer CropScience needed to provide a solution consisting of production equipment run by cloud-based software. The company calls the solution “On Demand Seed Treatment.”
To run the solution, seed treatment companies need modern production equipment that would allow them to both mix and apply the chemicals accurately. The solution also needs to accurately track which active ingredients were being added, to which seeds, at the retail level.
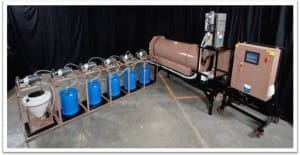
The equipment includes PLCs to ensure accurate mixing and a specified rate of application, and comes with pre-loaded bulk chemical kegs eliminating exposure to chemicals.
The software that runs the equipment — the iFix SCADA solution from GE Intelligent Platforms — is cloud-based. This application includes the master recipe system. Before seeds are treated, the seed retailer must select a recipe from the master system. The retailer scans a bar code on a chemical keg before connecting it to the machine to insure the right active chemicals will be applied. If they load the wrong keg, the system will not allow them to proceed.
Since the On Demand Seed Treatment is a single-instance, multitenant solution, better real-time information is available to growers, distributors, and Bayer CropScience. Specific benefits include:
- At the time of purchase, growers are provided with a batch treatment report, providing the data needed to improve their yields.
- Retailers now have the ability to apply chemicals to seeds in a process ensuring much higher quality levels.
- The On Demand solution can also track equipment reliability and tell seed treatment companies, for example, that a particular pump appears to have a flow problem.
- The cloud-based approach makes the process of providing updates, patches, and troubleshooting much easier.
- The application is integrated to Bayer CropScience’s SAP system. In the event of a recall, the batch numbers can be fed from SAP into the On Demand solution, allowing Bayer CropScience to handle the recall in a highly-targeted manner.
To ensure stewardship, Bayer CropScience requires seed treatment companies that want to sell its chemicals to purchase the On Demand solution. However, the company provides a variety of discounts to them.
Clearly, traceability projects don’t have to be driven by compliance requirements. They can deliver real benefits to both manufacturers and all key participants across an extended supply chain.
Leave a Reply