The benefits from Yard Management Systems (YMS) are driven by their ability to enhance five key processes within the yard. Here are some of the key benefits in those different process areas:
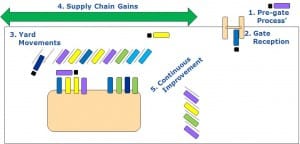
On-Line Dock Door Appointment Booking
A best practice, which is more common in Europe, is to have carriers book delivery appointments within a narrow window, the load is tipped on arrival, and the driver departs with an empty trailer. This practice is less common in North America, where yards are larger and can accommodate drop trailers waiting to be unloaded. Trailers tend to sit in the yard for a couple of days. However, having fully loaded trailers sitting in the yard acting as a safety buffer between transportation and warehouse processes is inherently poor practice.
Often, carriers book appointments by telephone, which can require a full time clerk, who handles between 200 and 300 appointments a day. A best practice is to have carriers or suppliers book appointments online. Leading yard management systems identify the best dock door for unloading and put-away, and enforce capacity constraints for that dock.
Gate Reception
Traditionally, a yard gate is manned by a security guard that tells inbound drivers where to park. The driver parks and then delivers his paperwork to the office. However, until these documents are processed, no one has visibility into what loads are currently sitting in the yard. Best practice automates this check-in process by eliminating unwieldy paperwork and inventory blind spots. In some cases, all that is required is a trailer and driver ID, which the system matches to data from the TMS and procurement systems to fully identify the load. The second benefit of logging in the truck at the gate is that the warehouse gets the earliest visibility that the load has arrived. If this load contains “out of stock” items, then the “live” load can be immediately routed to an inbound dock, improving warehouse and supply chain performance.
Visibility of Loads in the Yard
Most yard managers have stories of finding trailers in the yard containing loads that they knew nothing about. Even worse, if the trailer is a reefer, then the fuel will have expired long ago and the load will be spoiled, which creates additional removal and disposal costs. The knock-on effect of losing a load probably means that there was either a stock-out in the warehouse, or a customer was short-shipped, and in both cases sales were lost.
Companies, especially those that have a problem with shrinkage, have a clerk audit what trailers are sitting in their yard every two hours. Yard management systems provide visibility of what trailers and what stock is actually sitting in the yard, obviating both problems.
Yard management systems can also provide visibility of reefer fuel levels, with alerts to inform managers when the reefer fuel is about to expire. Again, this proactive approach can dramatically reduce the number of spoilt loads.
Visibility of Upcoming Demurrage/Detention Charges
The ability to control container demurrage and trailer detention costs is a cost bucket that companies should and can manage better. The first challenge is the ability to identify containers and trailers that are about to incur additional charges, so that these can be unloaded and released in time. However, whether or not these containers and trailers should be unloaded depends on the current priority of the tasks in the warehouse. For example, bringing forward the unloading might result in delaying fulfillment of a customer’s order. Therefore, identifying the best action requires tight integration and coordination with warehouse processes.
Maximize Throughput Capacity of the Yard
For most yard managers, the number of daily ins and outs is increasing, and is unlikely to decrease. Particularly in Europe, where land close to highways or motorways is expensive, yards tend to be relatively small. The combination of improved dock door scheduling, and visibility of empty trailers sitting idle in the yard, enables yard throughput to be increased. Typically yard management systems generate a 20 percent throughput increase. The cost benefit of avoiding additional building construction or renting/acquiring satellite yards can often justify the investment in yard management systems.
(This posting is an excerpt from a white paper—“How to Improve Yard and Supply Chain Performance”—ARC published last year on behalf of Sterling Commerce. The author, Simon Bragg, identifies several other benefits of YMS and also discusses the benefits of buying an on-demand solution versus a traditional, internally-deployed solution. You can register to download the full report here under the Sterling Multi-Channel Fulfillment section).